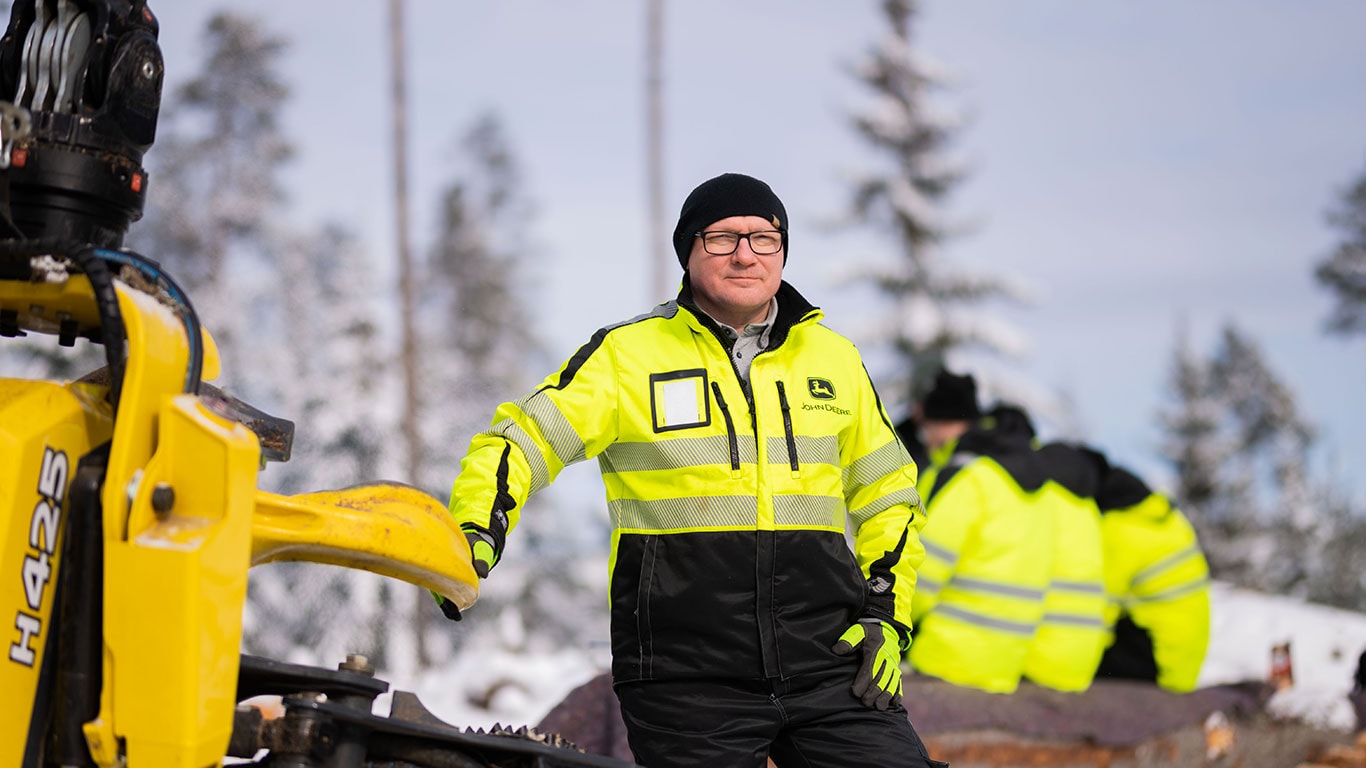
Engineering Team Leader Aki Pyykkö
The productization of a new forest machine series is a multi-phase process that takes several years at the very least. A peek behind the scenes of the engineering work reveals a team that is inspired by problemsolving, passionate about their work and isn’t deterred by the fact that their handprint takes years to see.
The outlining of a new series of forest machines starts as soon as the previous one is launched. But it takes a long time before it reaches logging sites. At the heart of the engineering work are constantly evolving customer needs, which John Deere pulls together from numerous sources, most importantly from its own customers and machine operators with whom Engineering Manager Timo Laitinen and Engineering Team Leader Aki Pyykkö interact with personally or through the support of the customer interface teams.
As customer needs arise around the world, they are inevitably very different. However, certain trends are prevalent regardless of the market. “For the machine owner, output is still the most important when working with the machine. But these days, having a machine that runs isn’t good enough; now it’s understood that operator wellbeing contributes to higher machine output,” says Laitinen.
The improvement in machine usability and workflow is a trend ending up on the drawing board of engineers from many angles. Northern Europe has long traditions of work wellbeing and ergonomics as such, but also the highly tuned production systems of South America require that the operator has the best possible conditions.
From engineering to testing and production
At John Deere, the engineering of a new series of forest machines is triggered by an annually approved portfolio plan. A new review is currently underway and is aiming for the turn of the decade.
“Until then, the game is pretty clear,” Laitinen notes. Some of the projects accepted for drafting are critical development projects that will bring completely new technology to the market. Therefore, also the productization cycle is longer.
“Designing new functionalities for a machine requires time both for the development and testing of the structure and the control system,” Pyykkö explains.
It takes cohesive teamwork to create a new series of forest machines. The 23-person engineering team for the forest machines, power systems and transmission is headed by Timo Laitinen, who keeps the ball rolling and ensures that targets are met. Team Leader Pyykkö leads the project for the harvesters and is responsible for the practical implementation together with the team. In addition to mechanical engineers, the project team includes frame, power systems and electrical engineers, as well as specialists in areas such as hydraulics and automation who are needed to implement each sub-project.
The project definition phase takes between one and two years. During this period, any new customer needs that have emerged are critically reviewed.
"Having a machine that runs isn’t good enough; now it’s understood that operator wellbeing contributes to higher machine output."
- Timo Laitinen -
Operators play a key role
John Deere’s forest machines end up in different environments where varying conditions affect the load on the machines and the way they are used. The design must take into account factors such as temperature, the steepness of the terrain, wood species, their weight and different assortments.
Even more significant than the environment is who is operating the machine. There are extreme examples to be found in every market: some operators take very good care of the machine and even take their shoes off when entering the cabin; others seek out maintenance only if the engine doesn’t start.
“The biggest differences in operating habits come from users with their different backgrounds, training, experience and preferences,” notes Laitinen. The level of operator training varies widely, and training isn’t even available everywhere. Many models are based on personal preference or ingrained habits rather than on technical grounds.
“A load of logs can be steadied against the headboard, putting stress on the headboard, or steadied on the ground, putting stress on the grapple mount. We have to take both into account.”
Motivated by the journey and the destination
When you only see your handprint every few years, you need other sources of motivation. What’s the best thing about designing new forest machines?
“Yes, I have a definite zeal for this work. I like looking at things from different angles and studying plans or 3D models. It’s so interesting,” Pyykkö admits.
Laitinen recognizes a number of motivating factors, both in himself and in his subordinates. For many, the main motivator is a high-tech product, the completion of which is not the only goal. Problem solving and learning along the way are equally rewarding.
“The high point, of course, is completing the product and hearing customer feedback, but that may not come for years after the actual effort. By that time, you may not be as excited about it since you are already preoccupied with new projects. For me, the most rewarding phase is the project definition phase: agreeing on what will be made,” says Laitinen.
TEXT: ANNE KASTARINEN, IMAGES: JOHN DEERE